A Comprehensive Overview to Welding Inspection: Understanding Standards, Techniques, and Finest Practices for Top Quality Guarantee
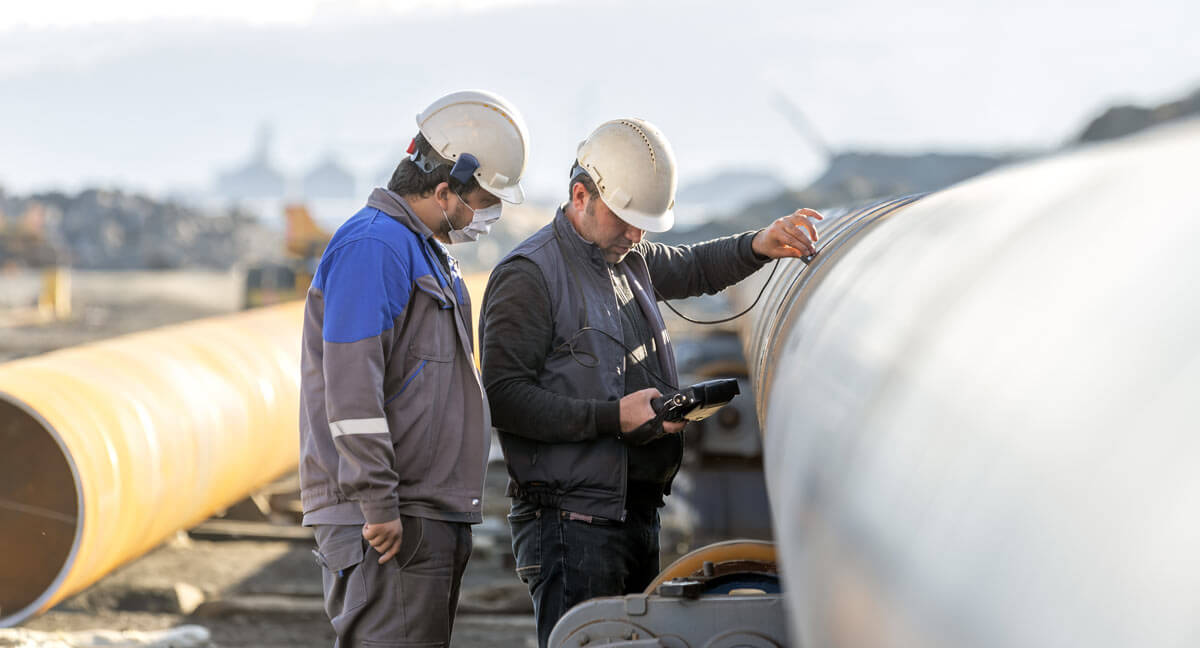
Welding assessment plays a crucial duty in making certain the architectural stability and safety and security of welded components, requiring a comprehensive understanding of industry requirements such as those established by AWS and ASME. Different inspection methods, including ultrasonic and aesthetic screening, are utilized to spot potential flaws that might jeopardize quality. In addition, implementing best practices can significantly enhance operational reliability and foster depend on among customers. As we discover these vital aspects, it ends up being evident that the effects of welding assessment prolong much past conformity, welcoming a more detailed examination of exactly how these processes shape market standards and methods.
Significance of Welding Assessment
Welding examination plays an important role in making certain the integrity and safety of bonded structures. It is a necessary process that confirms that welds adapt predefined requirements, which is vital in various markets, including construction, automotive, and aerospace. By conducting comprehensive evaluations, possible defects such as splits, incomplete combination, and porosity can be determined early, avoiding tragic failures that can bring about accidents or pricey repairs.
The significance of welding inspection expands past simple compliance with regulations; it additionally promotes trust with stakeholders. Customers and governing bodies expect guarantee that the frameworks they count on are developed to stand up to operational stresses. Moreover, effective welding evaluation practices add to long-term sturdiness and performance of the structures, ultimately leading to lowered maintenance costs.
In addition, welding inspection promotes a culture of top quality within organizations, encouraging adherence to finest methods and constant improvement. By integrating assessment processes right into the welding operations, companies can boost their track record and establish themselves as leaders in top quality guarantee. In conclusion, the significance of welding inspection hinges on its capacity to protect lives, make sure structural dependability, and copyright market standards, making it a crucial aspect of welding procedures.
Key Industry Specifications
Making certain compliance with vital market standards is important for preserving the high quality and security of bonded structures. Different companies develop these standards to promote best methods in welding and assessment. Among one of the most acknowledged are the American Welding Society (AWS) and the American Culture of Mechanical Designers (ASME), which offer thorough guidelines and specifications for welding processes and assessment requirements.
AWS criteria, such as AWS D1.1 for structural welding, rundown needs for products, layout, and screening to ensure the honesty of welds. Likewise, ASME codes, consisting of ASME Area IX, regulate the credentials of welders and welding treatments, making certain consistent top quality in industrial applications. Globally, the ISO 3834 common stresses high quality needs for combination welding, providing a framework for organizations to show conformity with worldwide best techniques.
Compliance with these requirements not only improves the integrity of bonded frameworks however likewise alleviates risks related to architectural failures. Moreover, adherence to industry criteria is usually a prerequisite for governing approvals and can substantially affect task requirements. Ultimately, understanding and applying these vital criteria are necessary for efficient welding evaluation and quality guarantee.
Examination Techniques Introduction
Efficient welding assessment depends on a selection of strategies developed to analyze the top quality and stability of welds. These strategies can be generally classified into non-destructive and devastating screening (NDT) approaches. Non-destructive screening strategies, which are extensively chosen in the industry, permit the examination of welds without compromising the integrity of the material.
Amongst the most commonly made use of NDT methods are aesthetic inspection, ultrasonic screening, radiographic screening, and magnetic bit screening. Visual evaluation is typically the primary step in the assessment procedure, making it possible for examiners to recognize surface area flaws and examine weld bead accounts. Ultrasonic screening uses high-frequency sound waves to discover internal flaws and gauge the density of welds. Radiographic testing entails making use of X-ray or gamma-ray imaging to expose inner issues, while magnetic particle testing is efficient for identifying surface and near-surface gaps in ferromagnetic materials.
Each method has its very own benefits and constraints, making it necessary for assessors to choose one of the most proper method based on the particular requirements of the task, the materials entailed, and the urgency of the welds being evaluated. This cautious option guarantees extensive evaluations and upholds safety and security and high quality standards in welding procedures.
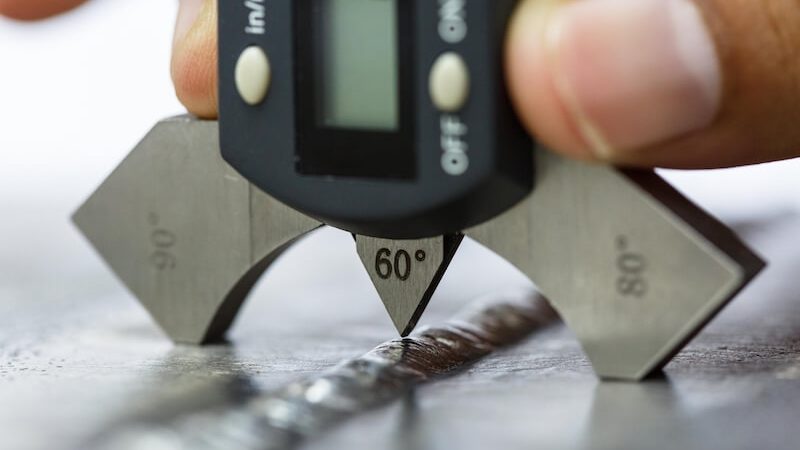
Usual Defects and Their Ramifications
A thorough understanding of typical defects in welds is vital for keeping architectural honesty and security in welded building and constructions. Welding problems can significantly jeopardize the mechanical properties of the joint, leading to failures that could jeopardize both personnel and devices.
Common flaws consist of porosity, which manifests as tiny gas pockets caught in the weld metal, deteriorating the total framework. Fracturing is one more common issue, typically arising from quick air conditioning or inappropriate joint layout, causing tension focus that can result in catastrophic failings. Insufficient blend occurs when the weld steel falls short to properly bond with the base material, creating weak points that might bring about separation under load.
Various other significant defects include undercutting, where the weld grain deteriorates the base metal, and slag inclusions, which can hinder the weld's strength. Each of these flaws has specific effects; as an example, porosity can reduce ductility, while cracking directly influences tensile stamina. more helpful hints Identifying and comprehending these issues during evaluation is important for carrying out corrective measures and making sure conformity with sector requirements, ultimately securing the architectural honesty of welded settings up.
Best Practices for Quality Control
Carrying out finest techniques for top quality guarantee in welding procedures is vital for attaining helpful hints ideal outcomes and reducing issues. One important practice is the facility of clear welding treatments that comply with industry criteria and specifications. These treatments need to include detailed directions concerning material choice, joint preparation, and welding methods to guarantee uniformity and quality.
Normal training and accreditation of welding workers are additionally essential. Skilled welders who comprehend the relevance of quality control are more probable to produce sound welds. Additionally, executing a durable assessment program, including both aesthetic and non-destructive testing (NDT), can assist determine problems early at the same time, enabling timely corrective activities.
Documents plays a key function in quality control. Maintaining accurate records of welding fixings, specifications, and inspections makes certain traceability and liability. Utilizing sophisticated modern technologies such as automated welding devices can boost precision and minimize the capacity for human mistake.
Last but not least, fostering a culture of top quality within the organization urges workers to focus on top quality in their job. By adhering to these ideal methods, companies can improve the stability of their welding processes, ultimately bring about boosted product quality and minimized prices related to rework and repairs.

Final Thought
In final thought, welding assessment plays a vital function in ensuring the honesty and security of bonded structures. Adherence to vital industry standards, such as those established by AWS and ASME, is necessary for effective high quality assurance. Employing different assessment techniques permits the identification of typical flaws, thereby reducing prospective threats. By executing ideal methods, organizations can improve dependability, decrease upkeep prices, and cultivate count on amongst clients, inevitably adding to effective welding procedures.
Additionally, welding inspection promotes a society of high quality within organizations, urging adherence to finest practices and continuous renovation. In final thought, the value of welding assessment lies in Related Site its capacity to protect lives, ensure architectural dependability, and promote industry standards, making it a vital element of welding operations.
Amongst the most identified are the American Welding Culture (AWS) and the American Society of Mechanical Designers (ASME), which provide thorough guidelines and requirements for welding processes and evaluation standards.
Ultimately, understanding and executing these essential standards are vital for efficient welding examination and quality guarantee.
Efficient welding inspection depends on a selection of techniques made to analyze the quality and honesty of welds. - Welding Inspection Gilbert Arizona
Comments on “The Ultimate Checklist for Welding Inspection Gilbert Arizona: Ensuring Safety and Accuracy”